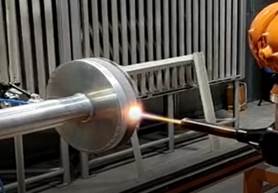
A new technique of synthesizing thin hard surface coatings by high velocity air fuel spraying, has the potential of emerging as an environment friendly safer alternative to hard chrome plating used in on car parts, tools, and kitchen utensils.
Chrome plating is used as it is hard and wear resistant. However, it consists of chromates, fluorites, and hexavalent chromium making it carcinogenic in nature.
This has initiated the researcher’s search for a safer, environment friendly alternative with an equivalent or superior wear resistance but crack-free coating.
Deposition of thin coating with industrially acceptable surface roughness is economical as it requires less powder and elimination of several grinding processes.
Thermal spray is a group of techniques to deposit wide variety of coatings for various industrial applications to reduce wear and tear and improve corrosion resistance.
While with conventional thermal spray techniques, thickness build up is high and several grinding and polishing operations are needed to acquire the required thickness and roughness.
A new technique called high velocity air fuel (HVAF), involving low temperatures and high particle velocities can deposit coatings using finer sized powders (5-15 µm).
Scientists from ARCI, an autonomous institution of the Department of Science and Technology (DST) carried out synthesis of thin hard coatings of a composite alloy of Tungsten, cobalt, and chromium (WC-10Co-4Cr) by high velocity air fuel spraying.
Thin coatings were deposited with torches with different capacities and by employing different nozzle sizes.
Coatings with 50 µm thickness and surface roughness’s close to 1.5 µm were achieved on stainless steel substrates.
The torch type and nozzle design influenced the coatings properties considerably.
Superior sliding wear performance was noticed with HVAF sprayed thin WC-10Co-4Cr coatings against conventional Hard Chrome Plating (HCP).
Similarly, corrosion studies carried out on the coating and compared with HCP showed that the new technique can be a better alternative to HCP for heavy load applications like hydraulic shaft, valves, piston rods, balls and so on.
A comparison of the hard chrome plating with as-sprayed thin cermet coatings to assess the performance of the latter showed that surface roughness of the as-deposited thin thermal sprayed WC-10Co-4Cr coatings is an order of magnitude higher than that of hard chrome plating.
Further, the coating can be deposited on as-machined condition to achieve smooth surface and around 50 µm coating thickness.
This significantly reduces the post coating finishing operations which reduces the processing and raw material cost significantly with better wear resistance than HCP.
The study published in the Journal of Thermal Spray Technology is expected to provide insights about the optimum thermal energy required without excessive surface melting and/or oxidation while retaining the dense microstructural features through sufficient kinetic energy for enhanced wear resistance.